A high-pressure air regulator valve is a valve that automatically cuts off the flow of gas or liquid when it reaches a certain pressure, allowing for safe and controlled pressure reduction. It is used to regulate and control the pressure of high-pressure fluid supply tanks or lines for various applications.
When a high-pressure regulator valve fails, it can result in air leakage and loss of control over the pressure. Common signs of a faulty pressure regulator include leakage, increased water and energy consumption, and high-pitched squealing. The difference between a pressure regulator and an air regulator is that a pressure regulator controls the pressure, while an air regulator limits the airflow.
Importance Of High Pressure Air Regulator Valve
Understand The Role Of High-pressure Air Regulator Valves In Maximizing Efficiency And Control
A high-pressure air regulator valve plays a crucial role in various industrial applications, where precise control of air pressure is required. These valves are designed to regulate and control the pressure of compressed air, allowing for efficient operation of pneumatic systems. By maintaining a consistent and specific pressure level, these valves ensure that equipment and processes perform optimally, leading to increased productivity and improved overall performance.
How They Regulate And Control The Pressure Of Air In Various Applications
High-pressure air regulator valves utilize a combination of mechanical and pneumatic principles to regulate and control the pressure of air in various applications. These valves typically consist of a diaphragm or piston mechanism that responds to changes in pressure and adjusts the valve accordingly. When the pressure exceeds the desired level, the valve opens to release the excess air, and when the pressure drops below the set point, the valve closes to allow more air in. This continuous adjustment ensures that the pressure remains within the specified range, providing precision control for different pneumatic systems.
Benefits Of Using High-pressure Air Regulator Valves
Using high-pressure air regulator valves offers several benefits in industrial applications, including:
- Improved Efficiency: These valves ensure that the compressed air is delivered at the optimal pressure, preventing energy wastage and minimizing system inefficiencies.
- Enhanced Equipment Lifespan: By providing consistent and controlled pressure, these valves protect pneumatic equipment from excessive strain, reducing the risk of damage and extending their lifespan.
- Precise Control: High-pressure air regulator valves allow for precise adjustment of pressure levels, enabling operators to fine-tune the performance of pneumatic systems according to specific requirements.
- Safe Operation: By regulating the pressure of compressed air, these valves contribute to the safety of industrial processes, preventing overpressurization and potential accidents.
- Cost Savings: Proper pressure regulation with high-pressure air regulator valves can result in energy savings and reduced maintenance costs by preventing system inefficiencies and equipment breakdown.
Overall, high-pressure air regulator valves are essential components in industrial pneumatic systems. They provide precise control, promote efficient operation, and contribute to the overall productivity and safety of various applications. By understanding their importance and benefits, businesses can make informed decisions when it comes to selecting and installing the right high-pressure air regulator valve for their needs.
Factors To Consider When Choosing A High Pressure Air Regulator Valve
Different Types Of High-pressure Air Regulator Valves Available In The Market
When it comes to choosing a high-pressure air regulator valve, it’s important to be aware of the different types available in the market. Each type of valve has its own unique features and benefits, so it’s crucial to understand what each type offers. Here are some of the most common types of high-pressure air regulator valves:
- Piston style regulator valves: These valves use a piston and cylinder to regulate the flow of air. They are known for their high accuracy and excellent control over pressure.
- Diaphragm style regulator valves: These valves use a flexible diaphragm to regulate the flow of air. They are commonly used in applications where sensitivity to pressure changes is crucial.
- Spring-loaded regulator valves: These valves use a spring to control the flow of air. They are simple and reliable, making them suitable for a wide range of applications.
- Pilot-operated regulator valves: These valves use a pilot mechanism to control the flow of air. They are often used in high-pressure systems where precise control is required.
- Relief valve regulator valves: These valves are designed to release excess pressure in a system to prevent damage. They are commonly used in safety applications.
Key Factors To Consider When Selecting The Right Valve For Your Specific Needs
Selecting the right high-pressure air regulator valve for your specific needs requires careful consideration of various factors. These factors will help you choose a valve that meets your requirements and performs optimally. Here are the key factors to consider:
- Pressure range: Ensure that the valve you choose can handle the maximum pressure of your system. It should have a pressure rating that matches or exceeds your requirements.
- Flow capacity: Consider the flow rate of your system and choose a valve that can handle the required flow capacity. It should have an appropriate flow coefficient (Cv) to ensure efficient operation.
- Materials: The materials used in the construction of the valve should be compatible with the type of gas or liquid being regulated. Ensure that the valve is made from high-quality materials that provide durability and resistance to corrosion.
- Size: Consider the physical size of the valve and ensure that it can fit into your system without any issues. Determine the connection type and size that is compatible with your system’s piping or tubing.
- Accuracy: Depending on your application, the accuracy of the valve may be crucial. Consider the level of precision required and choose a valve that offers the desired level of control.
- Reliability and maintenance: Look for a valve that is known for its reliability and requires minimal maintenance. It should be easy to operate and maintain, ensuring uninterrupted performance.
Importance Of Valve Materials, Sizes, And Pressure Ranges
The materials, sizes, and pressure ranges of a high-pressure air regulator valve play a crucial role in its overall performance and suitability for specific applications.
Firstly, the choice of materials is important because it determines the valve’s durability, resistance to corrosion, and compatibility with different gases or liquids. It’s essential to choose a valve made from high-quality materials such as stainless steel or brass that can withstand the pressure and conditions of your system.
Secondly, the size of the valve is significant as it should fit seamlessly into your existing system. Consider the physical dimensions and connection type of the valve to ensure a proper fit without any leakage or compatibility issues.
Additionally, selecting a valve with the appropriate pressure range is crucial to maintain safe and efficient operation. The pressure range should match or exceed the maximum pressure of your system to ensure accurate control and prevent any damage or failures.
In conclusion, considering the different types of high-pressure air regulator valves, key factors such as pressure range, flow capacity, materials, size, accuracy, reliability, and maintenance is essential in choosing the right valve for your specific needs. It’s important to evaluate each factor carefully to ensure optimal performance and longevity of your high-pressure air regulator valve.
Installation And Maintenance Of High Pressure Air Regulator Valves
Proper installation and regular maintenance are crucial for ensuring optimal performance and longevity of high pressure air regulator valves. By following the correct installation steps and implementing recommended maintenance procedures, you can extend the lifespan of your regulator valve and avoid potential issues. In this section, we will discuss the steps to properly install a high-pressure air regulator valve, recommended maintenance procedures and frequency, as well as tips for troubleshooting common issues.
Steps To Properly Install A High-pressure Air Regulator Valve
Installing a high-pressure air regulator valve requires careful attention to detail. Follow these steps to ensure a proper installation:
- Start by turning off the air supply and releasing any pressure in the system.
- Select the appropriate placement for the regulator valve, ensuring it is easily accessible for maintenance.
- Securely attach the regulator valve to the piping system using suitable connectors or fittings. Ensure proper alignment and tight connections to prevent leaks.
- Check the manufacturer’s instructions for any specific installation requirements or torque specifications.
- After the valve is securely installed, gradually open the air supply to allow pressure to build up.
- Monitor the pressure gauge on the regulator valve and make any necessary adjustments to achieve the desired pressure level.
- Perform a leak test to ensure there are no air leaks in the system. Apply a soapy water solution to all connections and observe for any signs of bubbling.
- Once the installation is complete and there are no leaks, you can resume normal operation of your high-pressure air system.
Recommended Maintenance Procedures And Frequency For Optimal Performance
To maintain optimal performance and prevent potential issues with your high-pressure air regulator valve, it is important to adhere to recommended maintenance procedures. Here are some key maintenance steps and their recommended frequencies:
Maintenance Procedure | Frequency |
---|---|
Inspect and clean the regulator valve | Every 3 months |
Check for any signs of wear or damage | Every 6 months |
Verify pressure accuracy using a calibrated gauge | Annually |
Replace worn or damaged parts | As needed |
Regular maintenance will help ensure that your high-pressure air regulator valve functions optimally and extends its lifespan. Consult the manufacturer’s guidelines for specific maintenance instructions and intervals.
Tips For Troubleshooting Common Issues With High-pressure Air Regulator Valves
Even with proper installation and maintenance, issues may arise with high-pressure air regulator valves. Here are some common problems and troubleshooting tips:
- Air leakage: If you notice air leakage around the regulator valve, check for loose connections and tighten as necessary. Inspect the valve body and seals for any signs of damage or wear. Replace worn or damaged parts as needed.
- Pressure fluctuations: Inconsistent pressure output may indicate a malfunctioning regulator valve. Ensure that the pressure adjustment knob is set correctly and inspect for any obstructions or clogs in the valve. Cleaning or replacing the valve internals may be necessary.
- Regulator creep: Creep occurs when the regulator fails to close completely, resulting in high-pressure air leakage. To test for creep, close the regulator to stop air flow downstream and gradually increase the air source until the desired delivery pressure is reached. If the pressure continues to rise, the regulator may require repair or replacement.
By following these troubleshooting tips, you can identify and resolve common issues with your high-pressure air regulator valve, ensuring optimal performance and safety.
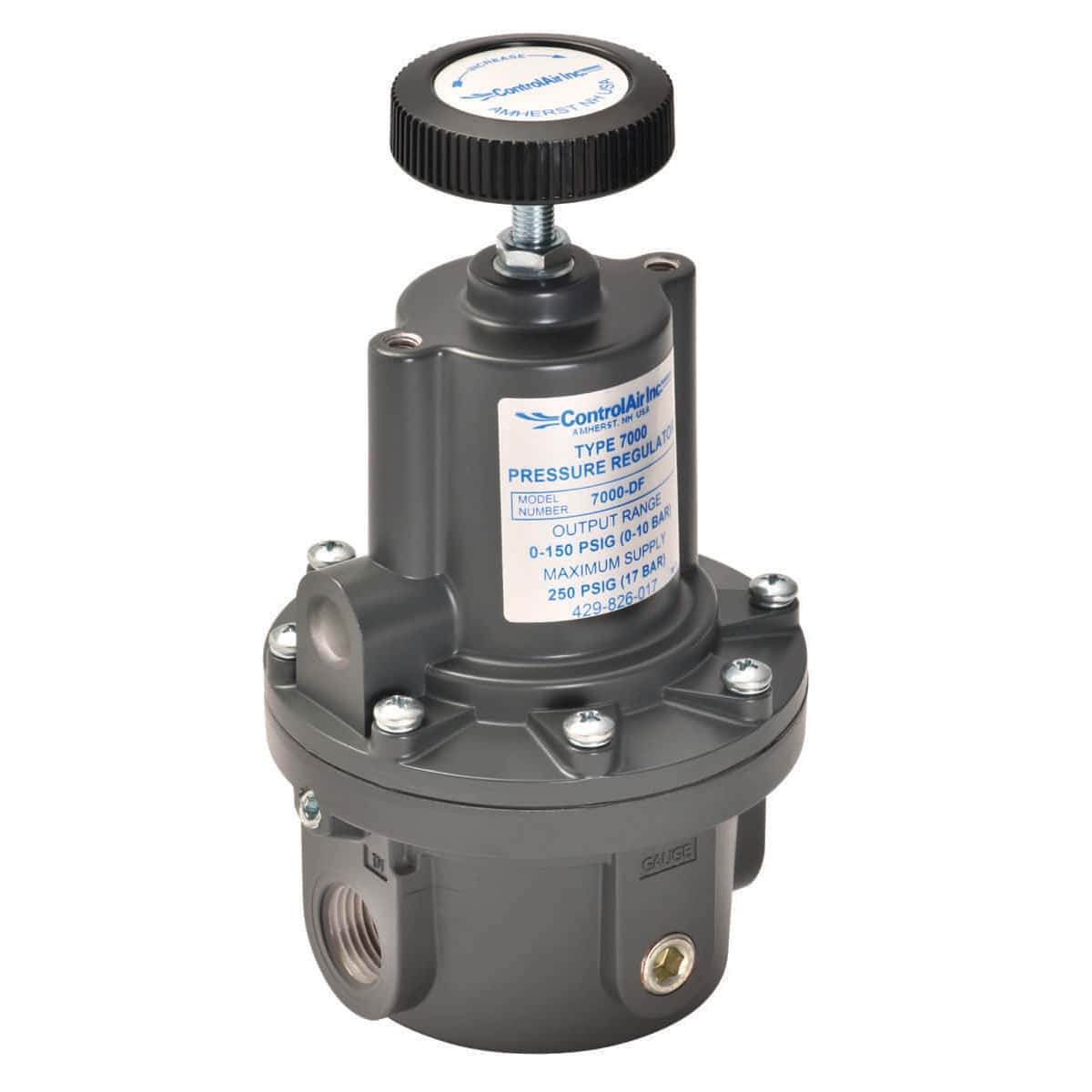
Credit: www.controlair.com
Safety Measures And Best Practices For Using High Pressure Air Regulator Valves
When working with high-pressure air regulator valves, it is crucial to prioritize safety. Following the proper safety protocols, handling and storing these valves correctly, and maintaining a safe working environment are essential for avoiding accidents and ensuring optimal performance. In this section, we will discuss the importance of following safety protocols, proper handling and storage techniques, and best practices for maintaining a safe working environment while using high-pressure air regulator valves.
Importance Of Following Safety Protocols When Working With High-pressure Air Regulator Valves
Following safety protocols is of utmost importance when working with high-pressure air regulator valves. These valves are designed to control the flow and regulate the pressure of air, which can be extremely dangerous if mishandled. To ensure the safety of yourself and others, it is crucial to adhere to the following safety protocols:
- Always wear appropriate personal protective equipment (PPE) such as safety goggles, gloves, and hearing protection.
- Inspect the valve and associated equipment for any damage or leaks before use.
- Ensure that all connections are secure and tight to prevent any air leakages.
- Follow manufacturer guidelines and recommended operating pressure limits.
- Never exceed the maximum pressure rating of the valve.
- Regularly inspect and maintain the valve to identify and address any potential issues.
Proper Handling And Storage Of High-pressure Air Regulator Valves
To ensure the longevity and safe operation of high-pressure air regulator valves, proper handling and storage are essential. Here are some best practices to follow:
- Handling:
- Handle the valves with care and avoid dropping or mishandling them.
- When transporting the valves, use appropriate containers or packaging to protect them from damage.
- Ensure that the valves are not exposed to extreme temperatures or harsh environments that can affect their performance.
- Always follow the manufacturer’s instructions for specific handling recommendations.
- Storage:
- Store the valves in a clean, dry, and well-ventilated area.
- Avoid storing the valves in areas with high humidity, extreme temperatures, or any corrosive substances.
- Keep the valves away from direct sunlight and sources of heat to prevent damage.
- Use appropriate storage racks or containers to prevent accidental damage or improper handling.
Best Practices For Maintaining A Safe Working Environment While Using These Valves
Creating a safe working environment is crucial to prevent accidents and ensure the efficient operation of high-pressure air regulator valves. Here are some best practices to maintain a safe working environment:
- Ensure that the work area is well-lit and free from obstructions.
- Keep the work area clean and organized, removing any debris or clutter that could pose a hazard.
- Regularly inspect and maintain all equipment, including hoses, fittings, and pressure gauges, to identify and address any potential issues.
- Train all personnel on the proper use and handling of high-pressure air regulator valves.
- Implement a comprehensive safety program that includes regular safety inspections, employee training, and emergency response protocols.
- Report any equipment malfunctions or safety concerns to the appropriate supervisor or maintenance personnel immediately.
By following these safety measures and best practices, you can ensure a safe working environment while using high-pressure air regulator valves. Prioritizing safety not only protects you and your colleagues but also ensures the efficient and effective operation of these valves.
Applications And Industries Utilizing High Pressure Air Regulator Valves
Various Industries That Rely On High-pressure Air Regulator Valves
High pressure air regulator valves are a crucial component in a wide range of industries, where precise control and regulation of air pressure is essential. These valves are utilized in industries such as:
- Manufacturing and Industrial: High-pressure air regulator valves are commonly found in manufacturing plants and industrial settings. They help maintain consistent air pressure for pneumatic tools, control systems, and automated machinery, ensuring smooth operations and efficient production processes.
- Construction and Infrastructure: The construction industry heavily relies on high-pressure air regulator valves to power pneumatic tools like drills, hammers, and nail guns. These valves enable precise control of air pressure, enhancing the safety and efficiency of construction projects.
- Automotive and Aerospace: High-pressure air regulator valves are integral to automotive and aerospace manufacturing processes. They are used in various applications like controlling air pressure in paint booths, powering air-powered tools on assembly lines, and regulating pressure in hydraulic systems.
- Energy and Utilities: In the energy and utilities sector, high-pressure air regulator valves play a crucial role in power generation, transmission, and distribution. They help control the flow and pressure of air in turbines, compressors, and pneumatic systems, ensuring optimal performance and safety.
- Chemical and Pharmaceutical: High-pressure air regulator valves are essential in chemical and pharmaceutical industries, where precision and control are critical. These valves are used to regulate air pressure in sensitive processes like batch reactors, fluidized bed dryers, and other pneumatic control systems.
- Food and Beverage: The food and beverage industry relies on high-pressure air regulator valves for numerous applications, including pneumatic conveying, air-driven mixers, and packaging machinery. These valves ensure consistent air pressure, contributing to efficient and safe food processing.
Examples Of Applications Where These Valves Are Commonly Used
High-pressure air regulator valves find applications in various industries and specific use cases. Some common application examples include:
- Pneumatic Control Systems: High-pressure air regulator valves are used in pneumatic control systems to regulate air pressure for precise control of actuators, valves, and other pneumatic devices.
- Pneumatic Tools: Construction, manufacturing, and automotive industries heavily rely on high-pressure air regulator valves for powering pneumatic tools like drills, sanders, grinders, and impact wrenches.
- Pressure Testing: High-pressure air regulator valves are used in pressure testing applications, where they help control and regulate the pressure applied to test specimens, ensuring accurate and safe testing processes.
- HVAC Systems: Heating, ventilation, and air conditioning (HVAC) systems utilize high-pressure air regulator valves to control the air pressure and flow for efficient operation and temperature control.
- Fluidized Bed Dryers: In industrial drying processes, high-pressure air regulator valves are critical for regulating the air pressure in fluidized bed dryers, ensuring proper drying of materials and preventing overheating or under-drying.
- Pneumatic Conveying Systems: High-pressure air regulator valves play a vital role in pneumatic conveying systems by regulating the air pressure to control the flow of powdered or granular materials through pipelines or ducts.
Case Studies Showcasing The Benefits And Efficiency Improvements Achieved With High-pressure Air Regulator Valves
High-pressure air regulator valves have proven to be instrumental in enhancing efficiency and achieving numerous benefits in various industries and applications. Let’s take a look at some case studies:
Case Study 1: Automotive Manufacturing
Problem: An automotive manufacturing plant was experiencing inconsistencies and inefficiencies in their painting process due to fluctuating air pressure.
Solution: The implementation of high-pressure air regulator valves allowed for precise control of air pressure in the paint booths, resulting in consistent paint application and improved finish quality. This significantly reduced rework and increased productivity.
Case Study 2: Chemical Processing
Problem: A chemical processing plant faced challenges in maintaining optimal pressure levels in batch reactors, leading to variations in product quality and production delays.
Solution: High-pressure air regulator valves were installed in the pneumatic control systems of the batch reactors, ensuring accurate pressure regulation throughout the production process. This resulted in consistent product quality, reduced downtime, and improved overall productivity.
Case Study 3: Construction Industry
Problem: A construction company was experiencing safety concerns and reduced efficiency due to inconsistent air pressure in their pneumatic tools.
Solution: By incorporating high-pressure air regulator valves into their pneumatic tool systems, the company achieved uniform air pressure across all tools, enhancing safety and improving the performance of their construction projects.
These case studies demonstrate the tangible benefits and efficiency improvements that can be achieved by implementing high-pressure air regulator valves in various industries and applications. Whether it’s ensuring precise control in manufacturing processes, enhancing the safety of construction projects, or improving product quality in chemical processing, high-pressure air regulator valves play a critical role in optimizing operations and achieving desired outcomes.
Frequently Asked Questions On High Pressure Air Regulator Valve
What Does A High-pressure Regulator Do?
A high-pressure regulator automatically cuts off the flow of gas or liquid when it reaches a specific pressure. It reduces high-pressure fluid supply to a safe level for different applications.
What Happens When A Air Pressure Regulator Valve Fails?
When an air pressure regulator valve fails, it can result in air leakage and failure to close properly, causing high-pressure air to escape. Signs of a faulty regulator include leakage, increased consumption of water and energy, and a high-pitched squealing noise.
An air pressure regulator limits the pressure export, while an air flow regulator controls airflow.
How Do I Know If My Air Pressure Regulator Is Bad?
Signs of a bad air pressure regulator include leakage, misting or overwatering, increased water and energy consumption, and high-pitched squealing.
What Is The Difference Between Pressure Regulator And Air Regulator?
A pressure regulator controls the flow of gas or liquid at a certain pressure. An air regulator specifically limits the pressure of the air being exported. The main difference is that a pressure regulator controls flow, while an air regulator controls pressure.
Conclusion
To ensure the proper functioning and safety of your high-pressure system, investing in a high-quality air regulator valve is essential. This valve acts as a control mechanism that automatically cuts off the flow of gas or liquid when it reaches a certain pressure.
By reducing the high-pressure supply to a usable and safe level, it ensures smooth operations for various applications. Additionally, monitoring your regulator for signs of failure, such as leakage or overwatering, is crucial to prevent any unwanted consequences. With a reliable high-pressure air regulator valve, you can optimize your system’s performance and ensure its longevity.