To wire a 240V air compressor, connect the black and white conductors to the breaker and ensure there is no neutral wire needed. The remaining steps can be found in various YouTube videos and forums dedicated to air compressor wiring, providing detailed instructions and diagrams.
These resources offer guidance on double-checking wire connections with a multimeter, testing the wire, checking the outlet, installing the faceplate, and adjusting the tank. Seek advice from professionals and consult the compressor’s manual for specific specifications.
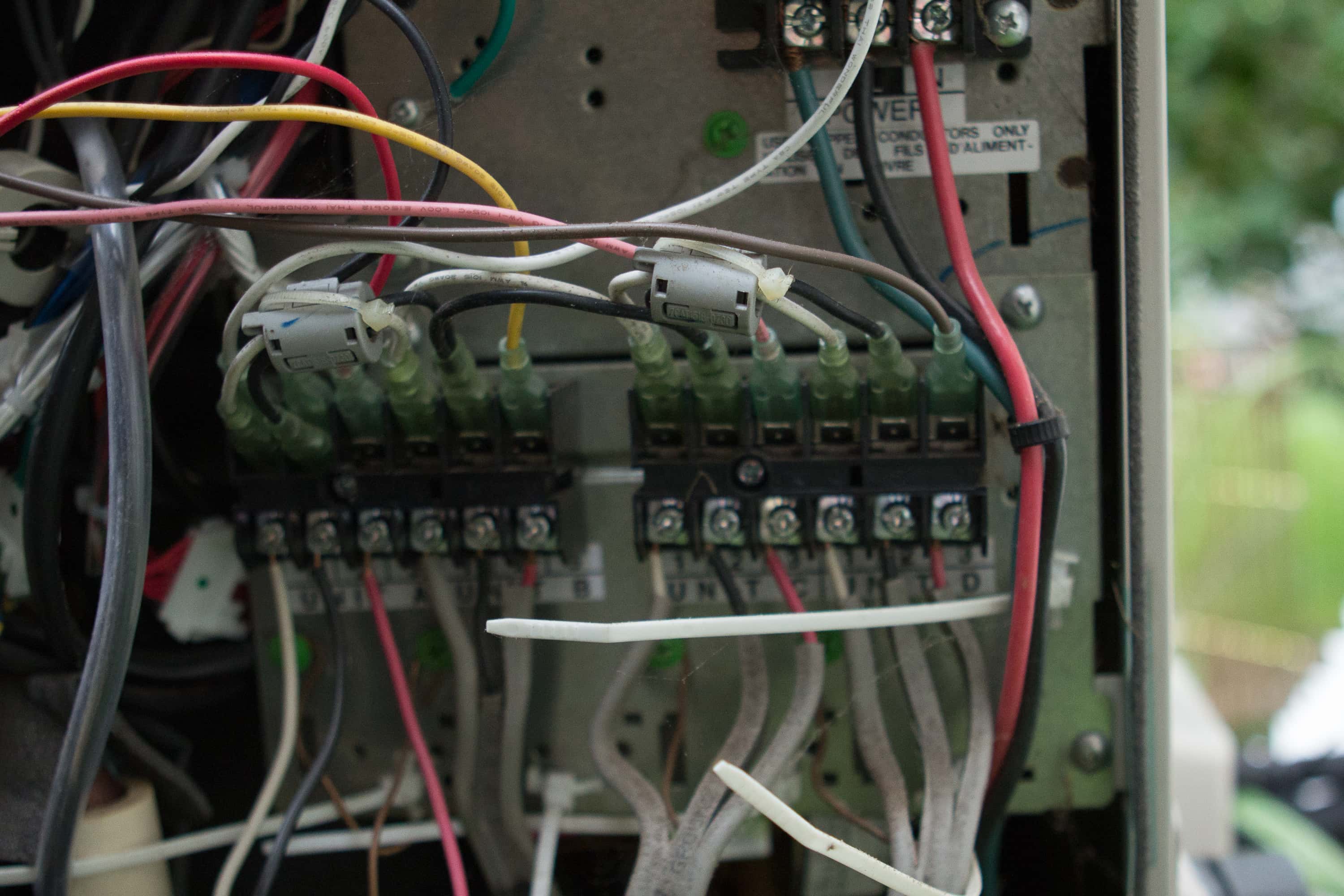
Credit: blog.totalhomesupply.com
Understanding 240V Air Compressors
What is a 240V air compressor?
An air compressor is a powerful tool that is used to convert electrical energy into potential energy stored in pressurized air. It is commonly used in various industries and households for tasks such as pneumatic tool operation, tire inflation, and spray painting. A 240V air compressor, as the name suggests, operates on a voltage of 240 volts, providing a higher level of power compared to standard 120V models. This increased voltage allows the compressor to generate greater air pressure and flow, making it suitable for heavy-duty applications.
Why do you need to wire a 240V air compressor?
Wiring a 240V air compressor is essential to ensure that it receives the correct power supply and operates safely and efficiently. Unlike smaller appliances that use standard 120V outlets, a 240V air compressor requires a dedicated circuit and specific wiring setup due to its higher voltage and power requirements. By correctly wiring the compressor, you can prevent electrical hazards, protect the motor from damage, and optimize its performance.
Important safety precautions
When dealing with electrical wiring for a 240V air compressor, it is crucial to prioritize safety. Here are some important precautions to keep in mind:
- Ensure that the power to the circuit is turned off before working on any wiring connections.
- Use appropriate safety gear, such as gloves and safety glasses, to protect yourself from potential electrical hazards.
- Verify the voltage and amperage requirements of your specific compressor model and select the appropriate circuit breaker and wiring size.
- Follow the manufacturer’s instructions and local electrical codes when wiring the compressor.
- Double-check the connections and wire terminations to avoid any loose or incorrectly connected wires.
- If you are not confident with your electrical wiring skills, it is recommended to consult a licensed electrician for assistance.
By understanding the basics of 240V air compressors and following the necessary safety precautions, you can confidently wire your compressor and ensure safe and efficient operation.
Tools And Equipment Needed
List of tools needed for wiring a 240V air compressor
When it comes to wiring a 240V air compressor, having the right tools and equipment is essential to get the job done correctly and safely. Here is a list of tools you will need to have on hand:
- Screwdrivers – both flathead and Phillips head screwdrivers will be necessary for removing and installing screws during the wiring process.
- Wire strippers – these tools are used to remove the outer insulation from electrical wires, exposing the copper conductor.
- Electrical tape – this tape is used to insulate and protect wire connections.
- Wire nuts – these small caps are used to secure and insulate wire connections.
- Multimeter – a multimeter is used to measure electrical voltage, current, and resistance. It is an essential tool for ensuring proper electrical connections.
- Pliers – pliers will come in handy when tightening wire nuts or securing wires.
- Wire cutters – these tools are used to cut electrical wires to the desired length.
- Label maker – having a label maker on hand will help you properly label wires and connections for future reference.
Required electrical equipment
In addition to the tools listed above, you will also need the following electrical equipment:
- 240V air compressor – make sure you have the appropriate air compressor for the job. Consult the manufacturer’s instructions for specific wiring requirements.
- 240V circuit breaker – you will need a dedicated circuit breaker rated for 240V to supply power to the air compressor.
- Electrical conduit – this protective tubing is used to encase the electrical wires, providing an extra layer of safety.
- Electrical wire – choose electrical wires that are suitable for 240V applications, such as 10-gauge or 12-gauge wires.
- Outlet and cover plate – select the appropriate outlet and cover plate for the air compressor’s electrical needs.
Safety gear necessary for the job
When working with electricity, it is important to prioritize safety. Here are some safety gear items that are necessary for wiring a 240V air compressor:
- Safety glasses – protect your eyes from any potential debris or sparks.
- Gloves – wear gloves to protect your hands from cuts or electrical shock.
- Ear protection – if your air compressor is loud, consider wearing ear protection to prevent hearing damage.
- Non-slip shoes – wearing sturdy shoes with good traction will help you maintain balance and prevent accidents.
Having the right tools, electrical equipment, and safety gear is essential when wiring a 240V air compressor. This will ensure that the job is done correctly and safely, allowing you to enjoy the benefits of your air compressor without any worries.
Step-By-Step Wiring Process
Wiring a 240V air compressor may seem intimidating, but by following a step-by-step process, you can ensure a safe and efficient installation. In this guide, we will walk you through each step, from locating the electrical panel to testing the wiring and ensuring proper grounding. Let’s get started!
Locating the electrical panel
The first step in wiring your 240V air compressor is to locate the electrical panel in your home or workshop. The electrical panel is usually found in a utility room or basement and contains circuit breakers or fuses for each electrical circuit in the building. Once you’ve located the panel, ensure that you have access to it and all necessary tools are nearby.
Choosing the appropriate circuit breaker
Before wiring your air compressor, you need to determine the appropriate circuit breaker size. The circuit breaker protects the electrical circuit and equipment from overloading. Consult the manufacturer’s specifications for your air compressor to determine the recommended circuit breaker size. Once you have that information, choose a circuit breaker that matches the recommended rating and install it in the electrical panel.
Determining the wire size and type
Next, you need to determine the appropriate wire size and type for your air compressor. The wire size is determined by the amps required by the compressor and the distance between the electrical panel and the compressor. Consult the National Electrical Code (NEC) or an electrician to determine the correct wire size for your specific setup. Additionally, ensure that you use wire rated for 240V applications.
Wiring the compressor pressure switch
Now it’s time to wire the compressor pressure switch. The pressure switch detects the air pressure inside the compressor tank and turns the motor on or off accordingly. Follow the wiring diagram provided by the manufacturer to connect the necessary wires to the pressure switch. Take your time and ensure that all connections are secure and tight.
Connecting the 240V outlet
Once the pressure switch is wired, you can proceed to connect the 240V outlet. The outlet provides the power supply for your air compressor. You’ll need to install the appropriate outlet box and follow the wiring diagram provided with the outlet. Make sure to turn off the power supply at the electrical panel before making any connections and double-check all connections before proceeding.
Testing the wiring and ensuring proper grounding
The final step in wiring your 240V air compressor is to test the wiring and ensure proper grounding. Use a multimeter or voltage tester to check the voltage at the outlet. Additionally, inspect all connections and ensure they are secure. Finally, verify that your air compressor is properly grounded by connecting a grounding wire to the designated terminal. Once you’ve completed these tests, you can safely power on your air compressor and start using it.
By following this step-by-step wiring process, you can confidently wire your 240V air compressor and ensure a safe and efficient installation. Remember to consult the manufacturer’s instructions and follow all local electrical codes to ensure compliance and safety. Happy wiring!
Common Wiring Mistakes To Avoid
When it comes to wiring a 240V air compressor, there are several common mistakes that should be avoided to ensure safe and efficient operation. These mistakes can lead to issues such as incorrect wire sizing, inadequate grounding, insufficient amperage rating, and improper installation of the pressure switch. To help prevent these issues, it’s important to understand the potential pitfalls and take the necessary precautions.
Incorrect Wire Sizing
One of the most common wiring mistakes when connecting a 240V air compressor is using incorrect wire sizing. The wire gauge you use should be based on the amp draw of your compressor and the length of the wire run. Using wires that are too small can lead to overheating and even fire hazards, while wires that are too large can be costly and unnecessary. Refer to the manufacturer’s guidelines or consult with a professional to determine the appropriate wire gauge for your specific compressor.
Inadequate Grounding
Another crucial aspect of wiring a 240V air compressor is ensuring proper grounding. Without adequate grounding, there is a risk of electrocution and damage to the compressor. To prevent this, make sure to connect the grounding conductor correctly and securely to a grounding rod or other approved grounding method. This will provide a safe path for electrical current to flow in the event of a fault or surge.
Insufficient Amperage Rating
Choosing a breaker with an insufficient amperage rating is a mistake that can lead to frequent tripping and potentially damage the compressor. It’s essential to select a breaker that can handle the amperage draw of your air compressor without exceeding its capacity. Refer to the manufacturer’s specifications and consult an electrician if you are unsure of the appropriate amperage rating for your compressor.
Improper Installation of the Pressure Switch
Proper installation of the pressure switch is vital for the correct operation of the air compressor. This switch controls the on/off cycle of the compressor based on the air pressure in the tank. Installing the pressure switch incorrectly can result in the compressor not turning on or off at the desired pressure levels. It’s important to follow the manufacturer’s instructions and wiring diagram carefully when connecting the pressure switch to ensure it functions correctly.
In conclusion, avoiding common wiring mistakes is crucial when wiring a 240V air compressor. Always use the correct wire sizing, ensure adequate grounding, select the appropriate amperage rating for the breaker, and install the pressure switch properly. By following these guidelines, you can ensure the safe and efficient operation of your air compressor.
Troubleshooting And Tips
How to troubleshoot and resolve common wiring issues
If you’re experiencing issues with your 240V air compressor wiring, fret not! In this section, we’ll discuss some common wiring problems and how you can troubleshoot and resolve them effectively. By following these steps, you’ll be able to ensure the proper functionality and operation of your air compressor, allowing you to work efficiently without any interruptions.
Here are a few common wiring issues you may encounter:
- Incorrect wire connections
- Faulty or damaged wires
- Inadequate wire size
When it comes to troubleshooting and resolving these issues, it’s crucial to follow proper safety precautions and consult professional help if needed. However, if you’re confident in your electrical knowledge and skills, you can attempt to resolve the issues yourself. Just remember, safety first!
Ensuring proper functionality and operation
Now that you’ve resolved any wiring issues, it’s essential to ensure the proper functionality and operation of your 240V air compressor. Here are a few steps you can take to accomplish this:
- Inspect all wire connections to ensure they are secure and tight. Loose connections can lead to overheating and cause damage to your air compressor.
- Use a multimeter to test the voltage at the compressor terminals. Ensure that you’re getting the correct voltage reading based on your compressor’s specifications.
- Check the pressure switch and ensure it is set correctly. This switch is responsible for automatically turning on and off the compressor based on the desired pressure levels.
By regularly inspecting these components and conducting maintenance checks, you can guarantee that your air compressor is operating at its optimal level.
Tips for maintaining your 240V air compressor wiring
Maintaining your 240V air compressor wiring is crucial for its longevity and performance. Here are some tips to help you keep your wiring in top condition:
- Regularly clean the area surrounding the compressor to prevent dust and debris buildup, which can affect the wiring connections.
- Inspect the wires for any signs of wear, such as fraying or exposed copper. If you notice any damage, replace the wiring immediately to avoid potential hazards.
- Avoid overloading the circuit by ensuring that the wire gauge matches the power requirements of your air compressor. Using the incorrect wire size can lead to overheating and electrical problems.
- Consider using surge protectors or voltage stabilizers to safeguard your air compressor from power fluctuations or surges.
Following these maintenance tips will help prolong the lifespan of your 240V air compressor wiring and ensure its reliable performance for years to come.
Frequently Asked Questions Of How To Wire A 240V Air Compressor Diagram
Does A 240V Air Compressor Need A Neutral?
No, a 240V air compressor does not need a neutral. The black and white conductors will connect to the breaker.
What Size Breaker Do I Need For A 240 Volt Air Compressor?
For a 240 volt air compressor, you will need a breaker with a size of 20 amps. The black and white conductors will terminate on the breaker without the need for a neutral wire.
How To Wire In 240 Volt?
To wire in 240 volts for your air compressor, follow these steps:
1. Connect the black and white wires to the breaker.
2. Make sure there is no neutral wire needed.
3. Double-check the connections with a multimeter.
4. Test the wire, check the outlet, and install the faceplate.
5. Adjust the tank as needed.
For a visual guide, you can watch tutorials on YouTube.
Can I Use 12 2 Wire For 240V?
Yes, you can use 12 2 wire for 240V. The black and white conductors will connect to the breaker.
Conclusion
To successfully wire a 240V air compressor, follow the steps provided in this comprehensive guide. Begin by identifying the colored conductors and connecting them to the appropriate breaker. Use a multimeter to double-check the wiring before testing the compressor and adjusting the tank accordingly.
Install the faceplate and outlet, ensuring safety precautions are followed at all times. This detailed diagram provides you with all the necessary instructions for a successful installation. Feel free to seek further advice and guidance to ensure your air compressor is wired correctly.